Introduction
What is a Mini Hydroelectric Generator?
A mini hydroelectric generator is a small-scale hydropower system that converts the energy of flowing water into electricity. These systems capture energy from small rivers, streams, irrigation canals or other water channels to generate renewable power for homes, farms, or communities.
Unlike massive hydroelectric dams that can impact rivers, mini hydro systems provide localized energy with lower environmental impact. They can range from just a few kilowatts up to 100 kW in capacity. This makes mini hydro an accessible way to harness the renewable power of water flow for personal or community use.
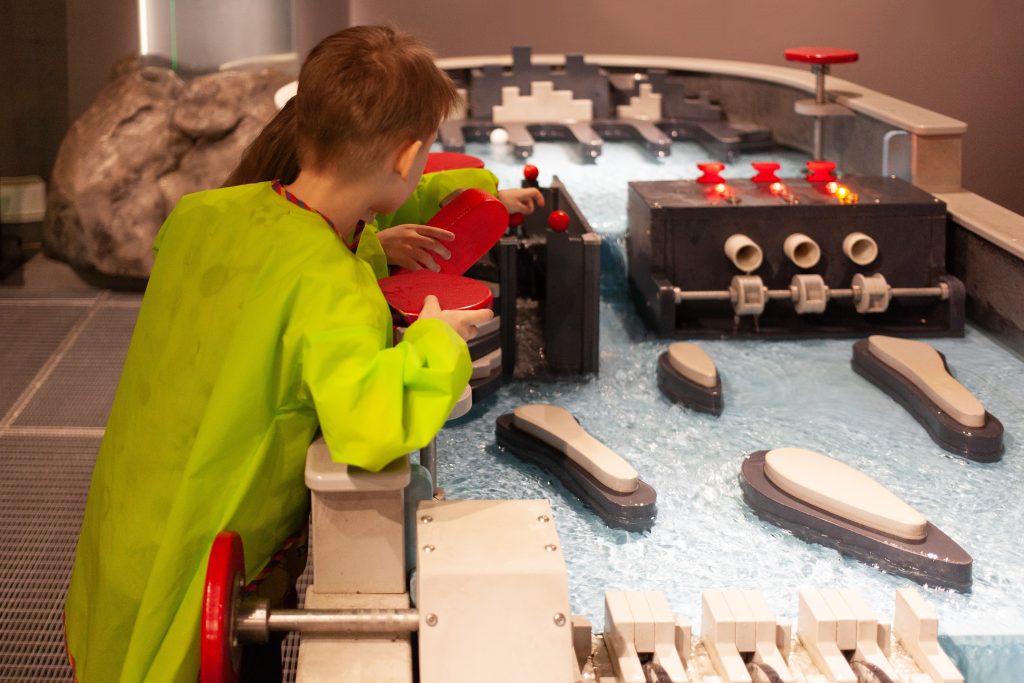
Benefits of Hydroelectric Power
Some key advantages of mini hydroelectricity include:
- Renewable and sustainable: Hydroelectric power is a clean energy derived from the continuous flow of water in nature. It does not produce greenhouse gas emissions.
- Energy independence: Mini hydro allows generation of electricity independently, reducing reliance on utility grid power.
- Low operating costs: Once built, hydroelectric systems have relatively low maintenance costs and the ‘fuel’ source (flowing water) is free.
- Revenue generation: Excess power can be sold back to the grid to make additional income.
- Reliability: Mini hydro provides a consistent supply of electricity in all seasons, unaffected by environmental factors.
- Low environmental impact: Small-scale systems have a low footprint and minimal disruption of local ecosystems compared to major hydro dams.
With proper planning and installation, mini hydro can be an efficient, cost-effective, and sustainable personal power solution. This guide provides a comprehensive overview of the entire process from start to finish.
Understanding Hydroelectric Power
Basics of Hydroelectric Energy
Hydroelectricity works on a simple mechanical principle: water flowing with force turns a turbine, which then spins a generator to produce electricity. The key components needed are:
Water flow – The ‘fuel’ for hydroelectricity. The water volume and flow velocity determines the system’s power capacity.
Turbine – The motion of water pushes and spins the turbine blades to rotate the shaft. Different designs (impulse, reaction, propeller, etc) are optimized for different site conditions.
Generator – Produces the electrical current. It can be turned by the rotating turbine shaft directly, or via a belt/gear transmission.
Penstock pipe – Transports water from the intake to turbine efficiently with minimum losses from friction.
Powerhouse – Houses the electromechanical equipment like turbine, generator, controls.
Tailrace/outlet – Discharges water after passing through turbine back into stream.
Battery bank – Stores excess electricity produced for later use.
Inverter – Converts generator’s AC power into usable AC electricity for off-grid systems.
Distribution lines – Carry the electricity generated to where it will be used.
This basic working principle can be adapted to many different scales and configurations, making hydropower a versatile technology. The components are optimized based on the particular site conditions and power needs.
How Water Turns into Electricity
Here is a simple overview of the mini hydroelectric power generation process:
- Water from a stream, canal, spring or other source is diverted through an intake into the penstock pipe. The intake system screens debris and fish.
- The penstock carries water to the mini hydro system’s powerhouse at an elevation drop. Gravity causes water to flow down with kinetic energy.
- The moving water hits the turbine blades in the powerhouse, making them spin like a water wheel.
- The turbine turns the metal shaft it’s connected to, which then spins the rotor of the generator.
- As its rotor spins, the generator converts the mechanical power into AC electricity.
- The electricity is regulated by controls and either used directly or sent to batteries for storage.
- For off-grid usage, the electricity has to be converted to usable voltage/frequency by running through an inverter.
- The water coming out of the turbine is discharged back into the stream through a tailrace.
- The cycle repeats to continuously harness the kinetic energy of flowing water into clean electricity.
The core principle is simple but engineering each component to work together efficiently requires thorough planning, material selection and testing.
Site Selection and Evaluation
The location of your mini hydro system is crucial for generating maximum power. Water flow characteristics and site conditions determine the hydropower potential.
Importance of Site Selection
- Selecting an optimal site makes your hydro system more productive and cost-effective. Poor site selection can lead to system underperformance, high costs and safety issues.
- The local terrain, water availability, intake height and presence of infrastructure are key factors to evaluate.
- Quantifying the water source’s flow rate and head (vertical drop) will indicate available energy at the site.
- Logistical factors like accessibility and permitting requirements also affect project feasibility.
- Environmental impact must be analyzed to minimize ecosystem disruption during construction and operation.
Careful site selection considering all relevant factors will help maximize power generation and economic viability.
Assessing Water Flow and Volume
The water flow volume and velocity through the system determines the power output capacity. Key parameters to measure are:
- Flow Rate – The volume of water passing per second measured in liters/sec, gal/min or cubic ft/sec. Direct field measurement gives accurate data.
- Head – The vertical drop that water descends through the system, measured in meters or feet. This drop harnesses gravity for water’s kinetic energy.
- Flow Duration – The perennial nature of flow. Seasonal consistency is ideal for year-round power.
- Water Velocity – Speed of water flow in the stream, canal or pipe measured in meters/sec. Faster velocity means more kinetic energy.
Data is collected across seasons to establish flow variability. Accurate hydrological measurements inform turbine size selection and help estimate annual power production.
Evaluating Site Accessibility
Easy access for transporting heavy equipment and construction is crucial:
- Road access for trucks should be available near the planned powerhouse and intake areas to allow delivery of components like turbine, generator and penstock pipes.
- If road access is not possible close by, ensure the site is reachable by construction vehicles or cranes for equipment delivery.
- Sites that are prohibitively difficult to access will lead to substantially higher transport and labor costs.
- Areas prone to flooding or unstable soils should be avoided to prevent damage.
- Grid connectivity for transmission lines should also be evaluated if selling excess power.
Choose a site with reasonable accessibility to key locations on the property to control costs.
Environmental Considerations
Any hydro development has potential for environmental impact. Careful planning minimizes ecosystem disruption:
- Do an environmental assessment to gauge habitat disruption, especially for endangered aquatic species.
- Maintain adequate water flow levels downstream of the intake to support wildlife. Avoid diverting full stream flows.
- Design intake grates to prevent entrapment of fish and debris.
- Consult with local wildlife agencies and follow regulations around stream water usage for hydropower generation.
- Select sites with minimal vegetation clearance required for infrastructure installation like penstocks and powerhouses.
Prioritizing environmental protection ensures your mini hydro project remains a green energy source.
Designing Your Hydroelectric System
Before construction, the hydroelectric system has to be custom-designed for the particular site conditions and power requirements.
Key Components Overview
The main components to be designed and sized are:
Intake – Collects and diverts water from stream into penstock pipe. Should minimize debris/silt intake and fish entrapment.
Penstock – Carries water to turbine under pressure. Size affects flow efficiency. Can be above or underground.
Powerhouse – Encloses the turbine, generator and control equipment. Must be accessible for maintenance.
Turbine – Converts kinetic energy of water into rotational energy to drive generator. Multiple design types available based on head and flow.
Generator – Uses magnetic induction to convert mechanical rotation into electrical energy. Output capacity matches turbine.
Tailrace – Discharges water from the turbine outlet back into stream.
Inverter – Converts generator AC power into usable home/grid electricity (required for off-grid systems).
Battery bank – Stores excess electricity produced for use when generation drops (for off-grid systems).
Each component must be optimally designed and sized for efficiency, safety and durability.
Turbine Types and Selection
Turbines are classified by operation principle and placement in reference to water:
- Impulse turbines – Water hits runner and changes direction. Used for high head sites.
- Reaction turbines – Water flows through runner and provides force. Used for low head sites.
Types include:
- Pelton wheel (impulse)
- Turgo turbine (impulse)
- Crossflow turbine (impulse)
- Francis turbine (reaction)
- Kaplan turbine (reaction)
- Propeller turbine (reaction)
Turbine selection depends on:
- Head – High head sites use impulse turbines while low heads use reaction turbines.
- Flow rate – The water volume throughput must match turbine’s hydraulic capacity.
- Speed – Match rotational speed to optimum speed of generator.
- Cost – Unit cost of turbine varies by type. Compare options.
Consult turbine manufacturers’ specifications to select the most suitable design based on your site parameters.
Generator Options
Generators convert the turbine’s mechanical power into electric current. Main choices are:
- Induction – Rotating magnetic field induces current flow in stationary conductors. Robust and low cost but needs capacitors for self-excitation.
- Synchronous – Magnetic field on rotor interacts with stator windings to produce current. Self-exciting but higher cost.
- Permanent magnet – Uses permanent magnets on rotor rather than winding exciters. Compact and no excitation loss but expensive.
Key factors for generator selection:
- Operating voltage and frequency match electrical distribution system.
- Output capacity matches expected turbine power.
- Compatible speed range for direct turbine coupling or determine gearing ratio needed.
- Generator efficiency rating and durability requirements.
- Budget constraints.
Careful generator choice ensures optimum electricity generation for your operating conditions.
The Role of the Penstock
The penstock pipe carries water from the intake to turbine under pressure. Design factors include:
- Material – Steel, HDPE and PVC are common options. Steel handles higher pressures but needs protection against corrosion. Plastics are easier to install but have lower pressure limits.
- Diameter and wall thickness – Must withstand water hammer pressures and prevent friction losses. Larger diameters minimize loss but increase material cost.
- Length – Longer penstocks require more materials but may be needed to reach suitable turbine location.
- Slope/elevation – Steep slopes allow shorter length but require anchoring against slippage. Gentler slopes increase pipe length.
- Buried vs. above ground – Above ground allows easier inspection but is vulnerable to damage. Underground has higher material costs for trenching but provides protection.
Optimized penstock design minimizes friction losses for efficient water delivery to the turbine.
Choosing the Right Inverter
For off-grid systems, an inverter converts the generator power into usable AC electricity for your home or business:
- Output wattage must meet all electrical load requirements. Choose inverter capacity for peak demand with headroom.
- Output voltage and frequency should match standard household current.
- Input voltage range must accommodate generator output which varies with water flow.
- Surge capacity should be at least twice the wattage for handling start-up loads from motors in appliances.
- Purity of sine wave affects compatibility with electronics and motors. Pure sign wave inverters are best.
- Safety certification is a must. Look for UL listing.
- Cost varies based on features. Balance your budget with operational requirements.
Selecting the properly sized inverter with essential features gives you usable, stable electrical power for off-grid living.
Tools and Materials
Constructing a mini hydro system requires some specialized tools along with common workshop equipment. Safety gear is also a must.
Essential Tools List
- Generator – Portable gasoline generator for powering tools and equipment
- Power drills – Cordless and/or corded drills for driving screws, holes, etc.
- Saws – Circular, jigsaw, handsaw for cutting pipes, wood, metal
- Wrenches – Adjustable, pipe, and metric wrench set for assembling turbines, penstocks
- Digging tools – Shovels, mattocks, pickaxes for excavation and trenching
- Measuring equipment – Tape measure, spirit level, screwdrivers, multimeter for electricals
- Safety gear – Hard hats, gloves, protective eyewear, dust masks, harness
- Flashlight – For inspecting dark enclosures and work sites
Renting specialty tools like trenchers or generators can save costs if you lack your own.
Tool Hire vs. Purchase
For specialty hydro equipment, consider renting vs. buying:
Pros of renting:
- Avoid large upfront costs of purchasing expensive tools.
- No maintenance or storage is needed for rented equipment.
- Can test tools on your site before committing to buying.
- Get access to a wider range of equipment models and brands to find the optimal tool.
Pros of purchasing:
- Tools are available whenever needed for the project timeline instead of rental availability.
- No recurring rental fees that can add up over an extended project.
- Can learn to master the tool over time instead of constantly switching rented equipment.
For items only occasionally needed in the project, renting makes economic sense. For essential tools, purchasing may be worthwhile if within budget.
Materials Checklist
Major materials and quantities required:
- Penstock pipes – Steel, HDPE, or other material. Diameter and lengths per design.
- Turbine and housing – Match model and size to your site’s head and flow rate.
- Generator – Voltage, capacity and enclosure per design. Typically induction type.
- Inverter – Output wattage matches electrical loads. Pure sine wave, UL-certified.
- Batteries – Sufficient capacity for off-grid storage. Deep cycle lead-acid typical.
- Land excavation/trenching materials – Gravel, etc. for creating stable foundations.
- Structural materials – Wood, concrete, steel for intake, powerhouse, and mounting structures.
- Electrical components – Wiring, disconnect boxes, conduits, breakers, outlets, etc. per electrical code.
- Plumbing fittings – For penstock, intake, spillway and tailrace connections.
Always order 10-20% extra quantities to account for waste, damages and unforeseen needs.
Safety Gear Recommendations
Personal protective equipment for mini hydro construction includes:
- Hard hat – Protects from falling debris, bumps and collisions. Essential for most tasks.
- Safety glasses/goggles – Prevents eye injuries from flying particles when digging trenches, cutting materials and using power tools.
- Hearing protection – Ear plugs or muffs shield from loud noise like generators or heavy machinery. Prevents long term hearing loss.
- Gloves – Leather, rubber or cotton gloves protect hands from blisters, cuts and abrasions.
- Dust mask – Important when working around concrete, soils and silica dust which are hazardous to inhale.
- Boots – Steel toe boots with grip avoid crushed toes and slips on slippery terrain. Waterproofing helps in wet conditions.
- Work clothing – Durable, snug clothes prevent entanglement in machinery. Bright colors increase visibility.
- PFDs – Personal flotation devices for any work near or in water to avoid drowning.
Taking precautions with safety gear prevents painful, costly and life threatening accidents on the hydro project. Don’t take shortcuts here.
Turbine Construction
For many homeowners, purchasing a pre-made turbine is the easiest option. But constructing your own turbine can be a satisfying do-it-yourself endeavour that saves costs.
Understanding Turbine Dynamics
Some key principles in turbine mechanics:
- The force of water impacting or flowing through blades produces torque to spin the rotor.
- Number and curvature of blades balances torque and rotation speed.
- Nozzle design on impulse turbines focuses water jet for maximum force on buckets.
- Runner diameter sizes torque production to the site’s head and flow rate.
- Rotor shaft connects to generator to transfer mechanical power.
- Efficient bearings support and reduce friction in shaft rotation.
- Housing directs water flows smoothly onto the turbine.
- Draft tube in reaction turbines helps decelerate discharge water.
Optimized turbine design maximizes rotational force extraction from the available water power.
Blade Design and Materials
For homemade turbines, blades can be fabricated from various sheet materials. Considerations for blade shapes and angles:
- Number of blades chosen creates optimal rotational speed. 3-6 common.
- Curvature and pitch angles affect water contact angle and torque.
- Cupped blades on impulse turbines catch perpendicular water jets.
- Planar blades on reaction turbines mount parallel to flow direction.
- Computer modeling helps refine blade shape and angle for performance.
- Stainless steel has high strength and corrosion resistance. Fiberglass resists erosion.
- Aluminum is lightweight but more prone to pitting over time.
- Cutting precision is needed to achieve uniform blade shapes.
With careful planning and fabrication, homemade blades can rival commercial turbine efficiency.
Assembling the Turbine Housing
The turbine housing or case encloses and protects the core components. Construction tips:
- The housing mounts and aligns the rotor shaft, bearings, seals and nozzle parts.
- Main housing can be welded or bolted steel plate for durability. Access doors are included for maintenance.
- Bearing mounts need precise alignment and structural rigidity. Poor alignment causes vibration and wear.
- Spiral casings on reaction turbines distribute water evenly around runner.
- Draft tubes create smooth water flow deceleration to minimize turbulence downstream.
- Accurate leveling and assembly ensures efficient operation free of leaks and imbalances.
Proper housing construction prevents premature turbine failure and minimizes power losses.
Connecting to the Generator
The turbine and generator shafts must be aligned and coupled:
- Direct coupling attachments like flanges, sleeves, and clamps allow shaft alignment adjustments.
- Flexible couplings accommodate small misalignments. But precise alignment is still essential for smooth power transfer.
- Belt or chain drives can enable speed adjustment between turbine and generator but have some power transmission loss.
- Generator is often offset from turbine and connected via shafts with bearings for convenient access.
- Larger turbines may need a gearbox to step up rotational speed to match generator RPM.
Proper turbine-generator interfacing ensures maximum power conversion efficiency.
Building the Penstock
The penstock piping is the water conveyance backbone of the hydro system. Well-designed installation prevents major energy losses.
Importance of a Strong Penstock
As the pressurized water delivery system, the penstock must withstand:
- High static water pressure from elevation drop without leaks or bursts.
- Surges from valves opening and closing that stress pipe joints.
- Vibrations and movements that fatigue materials over time.
- Corrosion and erosion, especially at intake.
- External damage from rocks, debris and vehicles.
- Freezing damage if above ground in cold climates. Underground burial is better protected.
Careful penstock engineering and construction prevents costly failures down the road.
Material Options and Selection
Common penstock pipe options:
- Steel – High strength for pressure, but needs anti-corrosion coating and expansion joints. Avoid galvanized steel.
- HDPE (plastic) – Lightweight, not corroded, good friction coefficient. But UV and impact sensitive above ground.
- PVC – Lower max pressure than HDPE. Must be buried to avoid UV damage. Low cost.
- Fiberglass – Corrosion resistant and good frictional flow. More expensive.
- Wood – Historically used but prone to leaks and short lifespan. Not recommended.
Consult manufacturer’s pressure ratings to aid material selection.
Laying and Securing the Penstock
Proper penstock installation and anchoring prevents damage:
- Buried pipes need graded trench with stone bedding for support and drainage.
- Above ground pipes securely fastened with saddles/hangers on metal/concrete pillars for anchoring against water hammer forces.
- Allow pipe expansion and contraction using expansion joints so pipes don’t warp or buckle.
- Gasketed couplings makes watertight pipe joints. Avoid leaky joints which lower pressure.
- Drain and vacuum relief valves prevent pressure buildup and removes trapped air in line.
- Bury pipe below frost line if possible in cold climates.
Careful penstock installation protects your piping investment and maintains pressure efficiency.
Setting Up the Generator
The generator selection directly affects the amount of electricity produced and connecting load capacity. Proper installation is vital.
Generator Types and Their Differences
The most common generator options:
- Induction – Rotor magnetism induced by stator current. Simple and robust but needs battery for excitation.
- Synchronous – DC current in rotor winding creates magnetic field interacting with stator for power generation. Self-exciting.
- Permanent magnet – Uses permanent magnets on rotor rather than wound exciters. More complex but avoids excitation loss.
Key differences:
- Speed – Induction generators run at a fixed small range of turbine speed. Synchronous speed must match turbine.
- Efficiency – Permanent magnet designs are most efficient, followed by synchronous and induction generators.
- Voltage regulation – Synchronous generators have more stable voltage output as turbine speed varies.
- Fault tolerance – Induction motors can handle grid faults and short circuits better than synchronous.
Matching generator technology to your particular turbine size and grid interconnection needs ensures optimum electricity production.
Connecting the Turbine to the Generator
Accurately interfacing the turbine mechanics to the generator is crucial:
- Generator mount must have precision alignment with turbine shaft. Misalignment causes vibration and bearing wear.
- Direct flange mounting of shafts is common. Allows axial adjustments.
- Flexible rubber couplers accommodate small amounts of misalignment.
- Belt or chain drives can enable speed adjustment but have some power transmission losses.
- Larger turbines may need a gearbox to convert RPMs between turbine speed and generator synchronous speed.
Proper turbine-generator integration transfers the turbine’s mechanical power most efficiently into electricity.
Electrical Safety Precautions
Generator systems carry serious electric shock hazards. Safety steps:
- Use insulated mats and covers when working on generator wiring.
- De-energize and ground lines during service. Wait 5 minutes for discharge.
- Have accessible emergency stop switches near the generator to cut power quickly.
- Water exposure is dangerous. Ensure generator is in waterproof housing with proper conduit seals.
- Connect protective earth grounding rod to generator frame.
- Install overload, short circuit and ground fault protection devices.
- Use warning signs and barricade live equipment.
Take every precaution when handling generator wiring and connections. Electrocution can easily be fatal.
Electrical Systems and Wiring
Properly designing and installing the system’s electrical wiring is a key element for efficiency, capacity and safety.
Basics of Electrical Wiring
- System voltage matches generator output and household current standards – typically 120V or 240V AC single phase.
- Wire gauge sizes must handle the electric current load. Undersized wires cause excessive heat loss and fire risk.
- Use insulated copper wiring meeting electrical code standards. Aluminum wiring connections can corrode.
- Wires housed in protective conduit piping or raceways for physical protection.
- Circuit breakers, fuses, and disconnects incorporated for overload protection.
- Follow all electrical code grounding, bonding and spacing requirements for safety.
Correct electrical design and wiring installation prevents blackouts,shorts and shock hazards.
Connecting to the Inverter
For off-grid systems, the generator AC power connects to the inverter for conversion to usable household current:
- Inverter input voltage range must match generator output under all conditions.
- Wiring must handle maximum current inverter draw plus allowable safety margin without overheating.
- Isolator switch placed before the inverter enables safe shutdowns for inverter maintenance.
- Overcurrent protection like fuses or circuit breakers included in case of shorts.
- Physical connections must be robust and vibration-proof. Inverter will have terminals for generator input.
Proper inverter integration allows stable, efficient AC power output for your off-grid loads.
Setting Up Batteries for Storage
In off-grid installations, battery banks store excess hydro electricity:
- Deep cycle lead-acid batteries are commonly used given high amp-hour capacity and deep discharge ability.
- Multiple batteries connected in parallel to increase total storage capacity. Series connections raise voltage.
- Charge controller regulates battery charge current to prevent overcharging damage.
- Batteries wired to inverter DC input for charging and load supply when turbine output is down.
- Place batteries in ventilated, temperature controlled enclosure to prolong life.
Adequate energy storage enables uninterrupted electricity even when generation fluctuates.
Grid Connection vs. Off-Grid Systems
- Grid-connected systems feed excess electricity to grid, pulling supplemental power when needed. Requires interfacing with grid voltage and phase synchronization.
- Off-grid systems require batteries and backup generators but provide independence from utility. Allows use in remote locations.
- Grid-connected systems are simpler and can sell excess power but require utility approval and fees. Off-grid provides self-sufficiency.
Evaluate your location access, energy needs and independence preference when choosing system type.
Safety and Maintenance
Routine upkeep and quick issue resolution keeps your mini hydro system running smoothly for years. Safety awareness also prevents accidents.
Routine Maintenance Checklist
- Check intake screens and clear debris/silt clogging flow.
- Inspect penstock pipes and joints. Repair leaks immediately.
- Verify turbine operation doesn’t vibrate or make unusual noise.
- Check bearings and couplings for wear. Replace as needed.
- Test generator voltage and spin freely.
- Inspect battery terminals for corrosion and charge cycles.
- Check safety labels and signage are intact.
- Clear vegetation overgrowth around equipment and access paths.
- Lubricate necessary points per component manuals.
Following the manufacturer prescribed maintenance schedule maximizes power production and lifespan.
Common Issues and Troubleshooting
Low/no power output
- Debris clogging intake system. Clean screens.
- Leaks in penstock reducing flow. Repair joints.
- Turbine wear or damage. Overhaul or replace.
- Generator winding failure. Rewind or replace.
- Break in electrical wiring. Check connections.
Turbine vibration/noise
- Misaligned shafts or couplings. Realign interface.
- Damaged or eroded runner. Replace turbine.
- Debris collision. Shut off and clear intake.
- Loose mounting bolts. Tighten fasteners.
Penstock leakage
- Joint gasket deterioration. Replace gaskets.
- Corrosion damage. Patch or replace section.
- The frozen water line burst. Repair and insulate line.
Simple troubleshooting can fix many basic issues and prevent system failure.
Safety Protocols and Best Practices
- Always de-energize and ground lines before servicing electrical equipment. Wait 5 minutes for capacitors to discharge.
- Keep fire extinguishers nearby electrical and generator installations.
- Use proper protective equipment like insulated gloves and eyewear when working on wiring.
- Avoid working alone at the hydro site in case of emergency.
- Erect barriers and warning signs around heavy machinery, trenches and high pressure pipes.
- Monitor penstock for leaks and promptly repair any found.
- Maintain first aid supplies on site.
- Keep mobile communication available in case of emergency.
Make safety the top priority. Preventing accidents saves lives and avoids system downtime.
Environmental and Legal Considerations
Complying with regulations and minimizing ecosystem harm ensures good standing in your community.
Understanding Environmental Impact
Potential mini hydro impacts and mitigations:
- Reduced river flow between intake and outflow. Maintain adequate residual flow for aquatic life support.
- Trap hazards at water intake. Use fine screens and exclusions.
- Fish entrainment in turbines and pipes. Limit velocities under feet/second and have downstream escape paths.
- Erosion and sediment release from construction. Use silt fences and avoid work in wet season. Re-vegetate banks.
- Noise and visual impacts. Enclose loud equipment and use aesthetic fencing and landscaping.
Being mindful of environmental effects makes mini hydropower more compatible with nature and neighboring communities.
Necessary Permits and Licenses
Typically required approvals include:
- Building permits for powerhouse, dams, and other structural construction.
- Utility grid interconnection approval and net metering agreements to sell excess power.
- Water rights permit for diverting stream flows from state environmental agency.
- Local zoning and land use permits.
- Environmental assessments for runoff, erosion control, fish protection.
- Historic and cultural review if any impacted archeological sites.
- Forest service approvals if located on federal public lands.
Know your regulatory requirements and build timeline cushions for approval periods.
Working with Local Authorities
- Be transparent with project details and timeline when interacting with regulators. Don’t hide information that may come up later.
- Hire consultants early to handle technical permit paperwork if unfamiliar with the process.
- Address any concerns raised by neighboring community regarding noise, access roads, etc proactively.
- Maintain open communication channels with permitting officials for smoother application reviews.
- Follow all approval conditions such as minimum environmental water flows, screening requirements, etc.
Building goodwill with permitting authorities streamlines the project approval process.
Testing and Optimization
Thorough testing during the commissioning phase catches issues early on and provides data to maximize efficiency. Monitoring also gives performance insights over time.
Initial Testing Procedures
Steps for the commissioning process:
- Inspect all installation for conformity to plans and electrical/building codes.
- Check wiring thoroughly for tight, secure terminations and insulation integrity.
- Confirm adequate earthing system electrical resistance.
- Pressurize penstock and check for leaks.
- Run generator dry, then with turbines at various gate settings to confirm output voltages and frequency tolerance to nameplate.
- Interface generator to inverter and check electrical parameters like voltage regulation and harmonics.
- Introduce electrical loads step by step while monitoring performance.
- Make final adjustments to optimize power output like nozzle placements and gate settings.
Thorough testing uncovers issues before full operation and prevents early failures.
Monitoring and Data Collection
Long term monitoring provides insights on performance:
- Collect voltage, current, power output data across operating conditions. Logs performance over time.
- Monitor turbine RPM fluctuations and vibration to catch problems early.
- Track penstock pressure variations and look for growing spikes signalling leaks.
- Record stream flows and weather conditions to correlate with output.
- Note annual maintenance and repairs needed.
- Quantify availability and downtime incidents to improve reliability.
- Analyze efficiency metrics like generator loss, line loss and discharge control.
Good data empowers optimal operation control and timely maintenance for sustaining high performance.
Making Adjustments for Efficiency
Use monitored data to boost efficiency:
- Adjust turbine speed by changing nozzles, runner pitch or gearing to maximize output at given flow.
- Modify penstock diameter or roughness to reduce head losses if data shows an issue.
- Increase generator field excitation current to maximize power production if the voltage drops under load.
- Improve power factor closer to unity to minimize line losses.
- Regulate turbine flow intake to limit spillage waste during low demand periods.
Continuous efficiency improvements keep your system operating at the optimum productivity threshold.
Cost and Budgeting
Like other construction projects, creating a realistic cost estimate and budget is key for mini hydro success. Know your options to control spending.
Estimating Total Project Costs
Typical elements to factor into capital costs:
- Intake infrastructure – Screens, gates, intake building
- Penstock piping – Materials, excavation, installation
- Powerhouse building and foundation
- Turbine and generator equipment cost
- Monitoring and control equipment
- Electrical wiring and installation
- Civil works like access roads, fencing
- Engineering and permit fees
- Construction labor
- Miscellaneous supplies and expenses
Get multiple vendor quotes and look at the costs of comparable projects to dial in accurate budgeting.
Saving Money with DIY vs Commercial Units
Cost saving strategies:
- Construct civil works like piping, powerhouse yourself using local materials.
- Design and build your turbine and generator if skilled rather than buying a commercial.
- Use manual governing rather than automated.
- Go with basic meters and controls instead of advanced automation.
- Opt for direct AC use rather than adding batteries and inverter for simplicity.
When paying more makes sense:
- Having a certified turbine/generator vendor handle complex installation and commissioning.
- Advanced automation and telemetry equipment for remote monitoring of an unattended site.
- Backup battery bank for reliable off-grid power 24/7.
- Interconnection equipment meets all utility standards for selling power.
Factor in your construction skills and site accessibility when weighing DIY cost savings against vendor advantages.
Return on Investment and Break-Even Analysis
To evaluate financial viability:
- Estimate the capital investment required for the mini hydro installation with a safety margin.
- Project the annual operating and maintenance costs.
- Calculate annual economic benefits like energy offsets and power sales revenue based on your particular conditions and tariffs.
- Determine a simple payback period where cumulative benefits equal initial investment.
- For more nuanced, run projection scenarios using discounted cash flow analysis and net present value calculation.
Crunching the numbers gives you the full picture of profitability and helps secure financing.
Conclusion
Reflecting on the Hydroelectric Journey
Looking back at the installation process:
- The long planning and research phase pays dividends later by setting your project up for success.
- Adapting designs to site-specific conditions and having the flexibility to change plans helps overcome the inevitable challenges that emerge.
- Patience and perseverance is key in troubleshooting the myriad technical and logistical issues. The hydroelectric learning curve is steep!
- The satisfaction of commissioning the system and having it generate clean energy makes all the hard work worthwhile.
With its combination of nature’s power and engineering, hydroelectricity is a rewarding renewable energy pursuit if done properly.
The Future of Personal Hydroelectric Power
Some technology trends shaping small hydro:
- Sophisticated turbine designs like helical maximize energy extraction from low head sites previously unviable.
- Affordable permanent magnet generators improving DIY turbine-generator efficiency.
- Improved battery storage technology expanding off-grid system capabilities.
- IoT-enabled intelligent monitoring and control for convenient system oversight.
- Advances in power electronics and conversion efficiency optimizing small hydro integration.
- Policy incentives improving project economics as renewable energy is prioritized.
- Low-cost modular and kit-based turbines enable rapid deployment.
- Drone-based stream mapping and site assessment to identify potential locations.
- Growth of community-scale microgrids using local renewable sources like mini hydro.
Ongoing innovations will make small hydropower more accessible, efficient and affordable than ever.
Encouraging Sustainable Energy Practices
While hydropower development must balance environmental concerns, responsibly implemented mini hydro systems truly embody sustainability.
Some ways small hydro promotes greener energy use:
- Harnesses the incredible power density of water without combustion or mining.
- Can electrify rural communities in developing countries as a clean alternative to coal and wood burning.
- Pairs well with other distributed renewables like solar PV in complementary hybrid systems.
- Encourages conservation by generating energy from what would otherwise be wasted flow.
- Allows transition to electric vehicles charged from personal hydropower for zero emission transportation.
With its endless renewability, hydropower persists as a foundation for clean energy independence.
Building a mini hydroelectric generator takes considerable diligence and effort. But the reward is an emissions-free, renewable electricity source you can proudly call your own. Use this guide to embark on your own path to hydroelectric energy self-sufficiency.